Let us first clarify the terminology we will be using: This diagram illustrates the difference between CI (Continuous improvement) and FI (Focused improvement).
CI describes the day-to-day “continuous” activities by employees to improve all aspects of asset management. These are normally small incremental improvements across a wide front and based on recommendations, intuition, intelligence and the experience of a motivated group of employees.
FI describes the dedicated “focused” interventions to make a substantial improvement in a very specific aspect of asset management (eg excessive breakdowns or high number of accidents) through a structured process of problem solving.
We will address Focused Improvement in this module.
So what do we focus on?
Firstly, senior management needs to give direction in terms of the organisation’s strategic goals. We all need to focus on what is important for the organisation as a whole.
Another focus area is often where the most money is lost, based on a thorough loss and waste analysis. This could typically be lost income because the income generating equipment is not available, or it could be excessive costs due to material waste, high overtime or some other inefficiency.
The strategic goals are normally deployed to team level in order to give them direction and focus.
The important thing is that we need to mobilise and focus our limited available resources (time, funds and people) on areas where the organisation can gain the most benefit (like a laser beam). Everyone in the organisation should be clear about these focus areas and their improvement activities should be guided to be in line them.
If a piece of equipment is suddenly underperforming, far below the lower control limit of the specifications. A typical example is the MME of a production line which suddenly drops from 98% to 85%.If the costs or implications are significant, this situation will require further investigation. That is where our problem solving tools need to kick in.
Once we have identified the opportunities for improvement, we need to follow a structured problem solving process to achieve sustainable and effective improvements. We will be using the same steps as the Six Sigma methodology which is DMAIC. It gives a solid framework for problem solving, irrespective of the sophistication of the tools used. Beware of your instinctive nature to take short cuts and jump to conclusions without proper analysis! You will regret it afterwards!
Let’s now look at the first step – Define. Before we can find the root cause or solution, we need to understand the problems and associated facts better. We will do this by gathering the available information to define the problem effectively using what (happened), where (happened), who (involved), when, why and how (big/much/many) tools abbreviated as 5W1H.Here it is important to focus all efforts on the specific problem to be addressed by defining exactly what the problem is. Don’t be too vague. The objective is to focus the efforts of the problem solving team on the real problem and avoid any side issues. The usually asked questions are what should be investigated? How does it impact such as cost? What is the improvement target? When should it be improved? Who must investigate it? It is also necessary to define the team members, the target improvement and the time scales.
Now we move on to the second step - Measure: Remember to gather the information from specifications, the people involved, when it happened, and historical data from the EAMS. An important principle here is to look for the story behind the numbers. Use the Pareto principle and its importance in data analysis:
• 80-20 principle
• Plots factors from big to small
• Separates the “important few” from the “trivial many”
• Helps to focus efforts
• Do from different views, eg longest downtime, biggest cost, most frequent stops
The quote is a saying which is often used by Six Sigma Black Belts when they analyse a problem.
Once we have studied the data, we need to find the root cause(s) which is the 3rd step of DMAIC.
Here it is important to follow the golden thread of cause-effect analysis or 5 why or A3 analysis in which fish bone is a guiding analysis tool. When you have exhausted the process, you have found the “root cause”. One very popular technique for root cause analysis is the 5 Why. Here you keep on asking why (not necessarily 5 times) until you have found the root cause. Its strength is its simplicity, which makes it ideal for use on the shopfloor.
Quite often, we do not have a linear cause-effect thread, but multiple causes to an effect. In such a case it is acceptable to branch out into different cause-effect branches until there are multiple potential causes. In such a case, we will have to verify and eliminate some of these causes in order not to spend effort on fixing a non-applicable cause. Fishbone or Ishikawa diagram is used to brainstorm different potential causes to a problem, based on the six legged 6M framework: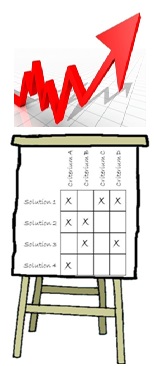
• Man (or person)
• Machine (equipment)
• Methods (process or procedure)
• Material (or component)
• Measure
• Medium (or environment)
We will also need to verify these potential causes and narrow them down to the real root causes before we implement step 4: Improve
These are the activities in the Improve step. The aim is to get an effective countermeasure to the problem.
-
Identify possible countermeasures
-
Select the most cost-effective solution(s)
-
Develop an implementation plan
-
Confirm logic of results
Another way of looking at the solution is to simplify it. Eliminate anything which could complicate matters:
-
Eliminate, combine, simplify.
-
Focus on the main issues.
-
Find a simple solution, that is effective.
This is the last step in the process to make a successful solution “stick”.
It is also important to roll out successful solutions to other areas. The Japanese call this “horizontal replication”.
-
Training
-
asset care plans
-
standard operating procedures
-
Modifications
-
Standardisation
... and roll it out to other similar areas
How do we ensure that problem solving is taking place at the right level with quick support by management if required? The solution is a “daily management system” which is a hierarchy of consecutive meeting on different levels in the organisation.
The process starts off with a daily morning meeting that is in line with our STO model. This could be a workshop meeting where the foreman discusses the breakdowns and major problems from the previous day or the night shift. Alternatively, it could be a shift handover meeting between the incoming and outgoing operational supervisors, and area technician. They would allocate major problems (eg downtime longer than 1 hour) to a small team for further investigation and solution.
If the problems are beyond their capability, there would typically be a meeting later in the morning, attended by middle management and support departments (eg Material Management, Central Workshop, Services, Engineering, etc) to provide support to the front line staff. They would typically look at more complex problems and systemic problems such as procedures or information systems.
If it becomes clear that the problem is not situational or systemic, but strategic, it needs to be referred to senior management level. This could typically be a weekly or monthly meeting where senior managers discuss supply chain issues, outsourcing, demand management, etc.
It is also important to give the teams feedback on progress and solutions.
Remember to measure and quantify the benefits from the FI projects. It will:
• monitor whether the targets have really been met
• confirm that the FI efforts are paying dividends
• give the team members a sense of achievement.
Remember to celebrate and recognise successful improvement projects. It will motivate the team members to improve even more.
So to summarise, this is what focused improvement is all about.
If this is a focus area for your organisation, ensure that everyone is trained in the more detailed techniques of structured problem solving and root cause analysis.