Planning definition
It is a "contract" between Sales and Production
It covers a short/medium-term period ( 1 - 6 months) with weekly itemization
Deciding
what to produce
which batches
sequences to adopt so as to allow production launch and material management(production capacity utilization)
It breaks the aggregate plan down into specific items with a higher level of detail on products and schedules
It acts as a buffer between Sales and Production
It steers the whole production and material management system
It drives purchasing and capacity checks
It provides information on customer order processing
Relationship between aggregate plan and Master Production Schedule
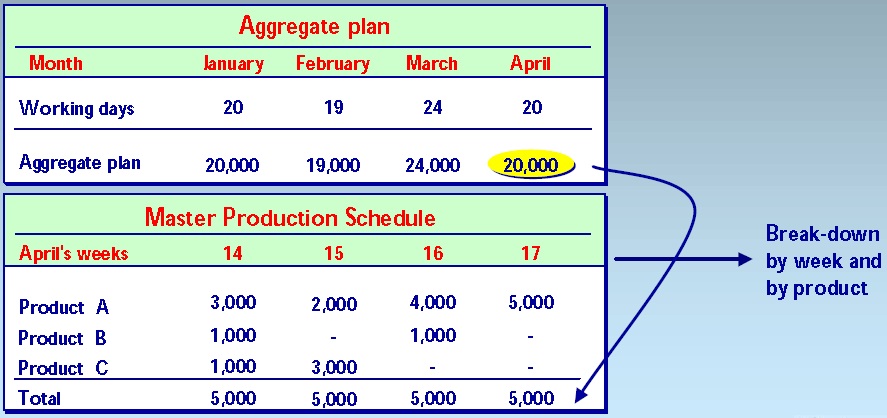
Planning horizon
The Master Production Schedule is developed for a period of time called" planning horizon".
The "planning horizon" should at least be as long as the longest cumulated lead time (CLT) plus a period of future "visibility".
Cumulated lead time is the longest period of time required to carry out product-making activities and it can be determined from the product's "timing" structure (bill of materials) by looking for the longest throughput time for each production step.
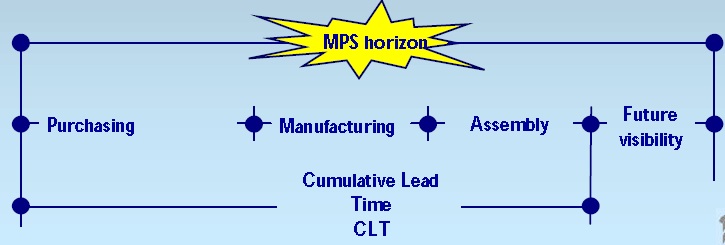
Planning hierarchy
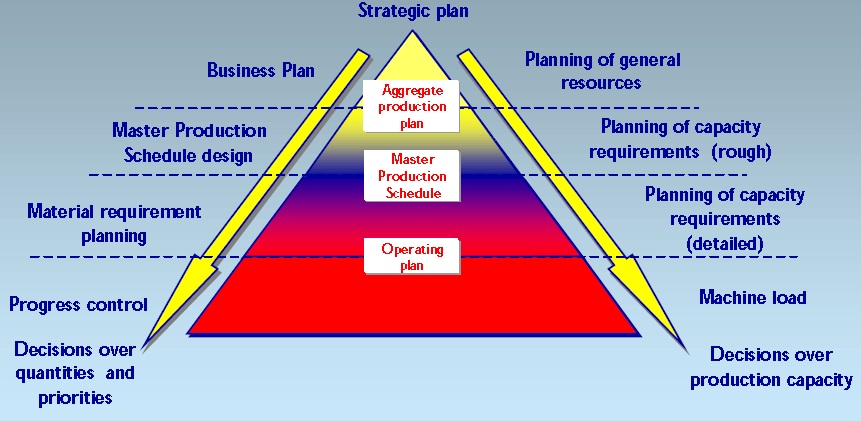
Planning management levels
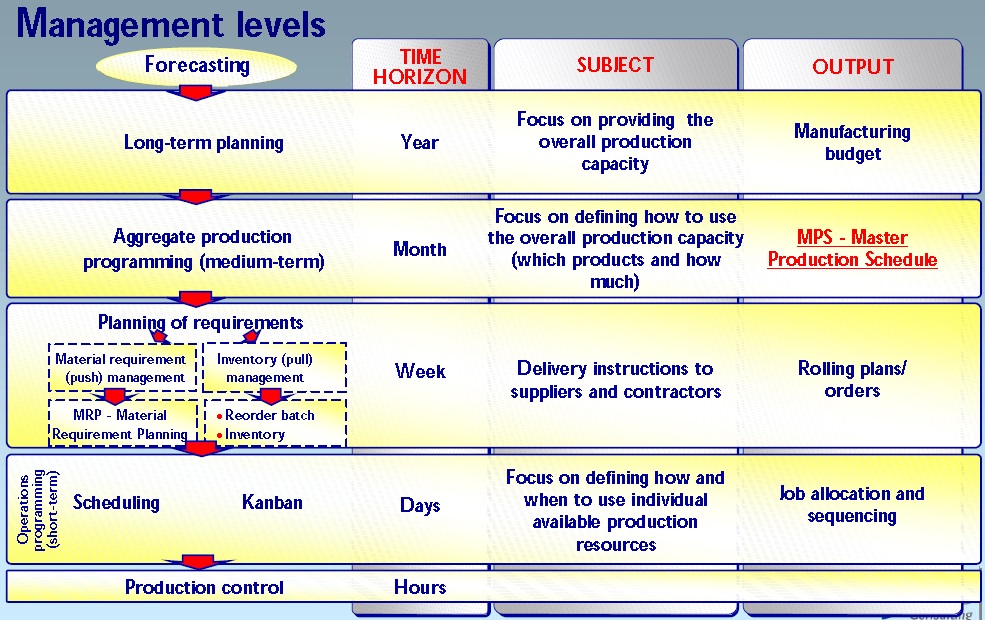
Master prodution schedule design-Variables to be considered
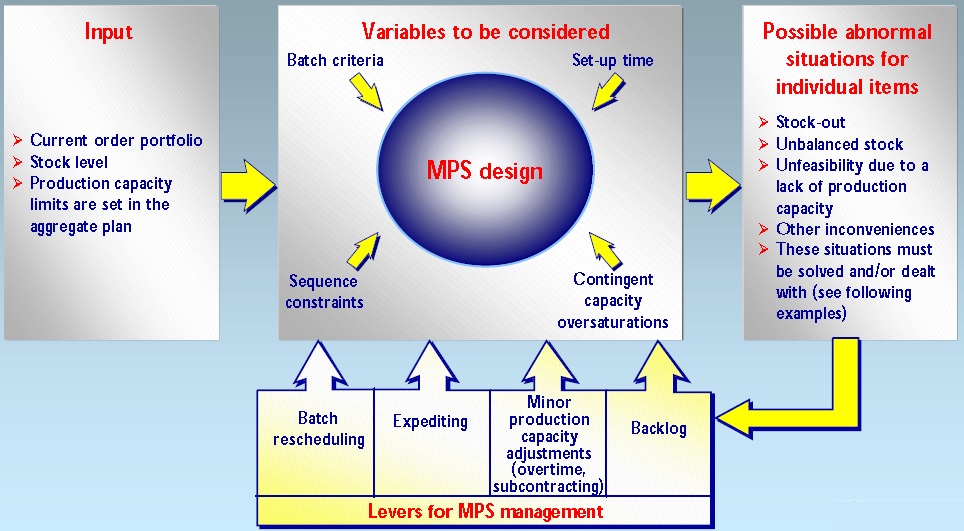
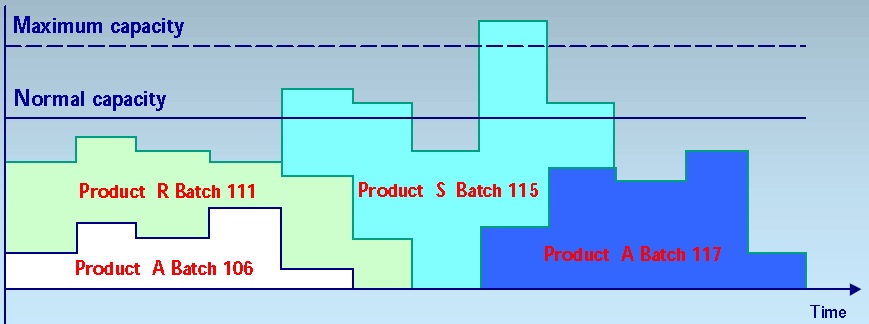